Today’s post covers CAD prosthetic designer cost, rates, and pricing for companies and individuals. Before the invention and rapid adoption of 3D printing, the only way to produce prostheses was by conventional casting, injection molding services, or combining those two. Either method requires a lengthy manufacturing process from the initial evaluation of a patient, measurement, cast production, socketing test, fitting, and cosmetic restoration. A prosthesis must undergo several iterations (prototypes) before the final product is ready.
Since each patient needs a custom model (or socket for a prosthetic limb), a new device must be made from a different mold. It was not until the late 1980s that the medical world began recognizing the huge potential advantages of CAD/CAM methods to produce prosthetic devices. When 3D printing came along, it became possible to reduce the total turnaround time and labor cost to a great degree.
RELATED: How 3D printed prosthetics are changing lives
One of the most time-consuming tasks in the conventional manufacturing process of prosthetic limbs is the socket design. Each socket is unique and made specifically for the individual wearing the device. It is through the socket that the wearer’s body weight is transferred or distributed as naturally as possible to the ground to reduce discomfort. For upper-limb prosthesis, there needs to be knee an artificial knee joint to improve mobility. Here, the expertise of a freelance CAD prosthetic designer comes into play, crafting personalized designs for prosthetic solutions.
3D Printed Prosthesis
World Health Organization estimates that only around 5-10% of people (approximately 1 out of 10) who need prostheses have access to those devices. Much of the problems are due to high cost and availability. A functional and customized prosthesis can cost $120,000 or more. Many amputees cannot even afford the $2,500 traditional barebone options manufactured with conventional molding without any additional functionality. Prosthesis manufacturing optimization by 3D printing design companies can cut the cost to a considerable extent.
RELATED: How the healthcare industry uses 3D printing and 3D bioprinting for treating patients
Financial constraints have always been the main problem that stands in the way of patients needing prostheses. In a world where only a tiny percentage of people who need prostheses have access to the devices, there needs to be a middle ground to ease accessibility without putting too much of a financial burden on the manufacturer or fabricator. And this is where 3D scanning services and printing come in.
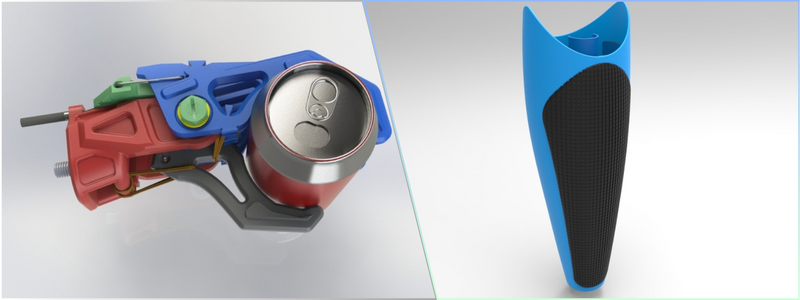
The cost of material to produce a prosthetic socket for adults amounts to only around $100, and the 3D printing process itself is $20; the cost only covers the manufacturing of the socket. It is worth noting that a transfemoral (above-knee) prosthesis also requires a knee joint and a structure called a pylon composed of lightweight metals or carbon fiber. Be that as it may, the total cost should not be anywhere near the $2,500 mark.
Let us say a shock-absorbing pylon and adapters are priced collectively at $200, a rotating knee joint with 100kg weight capacity at a conservative $300, and a simple artificial foot at a generous $200; the final product costs $820. With shipping and taxes, the maker can sell a complete device with a profit margin of $1000. Nearly all the design works are for the socket, while all other parts are ready-made. Of course, the prosthesis will not be as aesthetically pleasing or technologically advanced as its branded alternatives, but the functionality is all there.
RELATED: 3D scanning services: how much will it cost my company?
A smaller prosthesis, such as an ear replacement, should be even more affordable. Several years ago, researchers at the Queensland University of Technology proved they could manufacture an affordable soft tissue prosthesis using a low-cost desktop 3D scanner and printer. Silicone was the material of choice. All the consumables that went into the production process were worth no more than $3, and they paid $116 for two hours of labor. The researchers also built another version of the same prosthesis with a casting method using a 3D-printed ABS mold, which cost $155 for labor and consumables.
Either option was still more affordable than the traditional hand-crafted prostheses, ranging from $2,000 to $7,000 and taking at least 14 hours of labor. Everything sounds great, but there are a few potential drawbacks. 3D printing is not an instant process. While the scanning and designing processes are possibly done in just several hours, the printing alone may take 24 hours to complete. The prostheses are also limited in terms of material options. Chances are they are printed from PLA or ABS instead of powder metal, but it is necessary to sacrifice structural rigidity to save costs.
RELATED: How to design medical products that people actually want
Another downside is that not every 3D printing company might be technically qualified to build prostheses for medical purposes. Unless the prostheses are meant to replace soft tissues or for cosmetic purposes like ears and noses, the most qualified people to make the devices are licensed prosthetists and orthotists. Obtaining the license is not easy because they must complete a master’s degree in the field and obtain the certifications to practice. They are professionals trained to design and fabricate prescribed prosthetic devices. Adjusting, repairing, and replacing prosthetic devices are also parts of their duties.
Design Cost
The BLS says that the average median pay for prosthetists and orthotists (2022, latest data available) is $77,000 a year or around $37 per hour. Prosthetists specialize in artificial limbs and other body parts, whereas orthotists work on supportive devices such as knee braces. The good thing is that prosthetists and orthotists are utilizing 3D scanning and printing technologies to do their jobs.
RELATED: Medical device design: a guide to service pricing, costs, and rates for companies
Although their clinics likely don’t have a complete 3D printing facility, they can collaborate with prosthetic design services and local manufacturers to simplify workflow and reduce turnaround time. For example, the production of an above-knee prosthesis typically goes through the following steps:
- A prosthetist scans the patient’s residual limb at the clinic. 3D scanning is the most reliable technology to produce a 3D model of the mold (for the prosthetic socket). It will create a digital, accurate copy of the residual limb surface geometry and dimension for proper fitting. 3D scanning only takes a few minutes.
- CAD software transforms the scanned image into a custom 3D model. It might involve cleaning up and post-processing before the file can be converted into printable format. The step takes about 2 hours.
- The finished ready-to-print prosthesis model is sent to a 3D printing shop for manufacturing. The model should be ready in 2 – 5 business days after post-processing and cleaning up.
- The manufactured prosthesis is ready to use and sent back to the clinic. The overall turnaround time is between 1 – 2 weeks.
The first and second steps make for the biggest design tasks, where a prosthetist or orthotist scans and creates the 3D model of the device to be manufactured. The hourly rate mentioned above only covers those services. If priced on a per-project basis and done by Autocad design professionals (instead of prosthetist/orthotist), the cost for 3D scanning and conversion into print-ready 3D images typically falls in the $120 – $150 range.
RELATED: Cad Crowd 3D Design – Stay Healthy with Medical Product Development Services
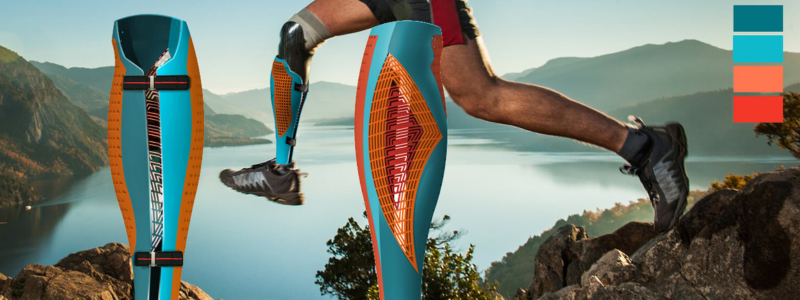
High-end 3D printing
Just because 3D-printed prostheses are more affordable than traditional injection-molded variants does not necessarily mean everything is cheap for everyone. Product options and prices are parts of a spectrum, so it is not entirely unlike other businesses. While it is possible to manufacture a functional above-knee prosthesis for under $1,000, the final product is likely a basic variant made of easily sourced material. It has the functionality of a prosthesis, and in many cases, nothing else is more important.
The business side of 3D printed prostheses runs from individual freelancers producing artificial limbs out of hard plastic to state-of-the-art facilities creating ISO-certified prosthetic devices. At the higher end of the spectrum, it is not uncommon to see above-knee carbon fiber or aerospace-grade aluminum prostheses. Companies operating at this level are essentially doing the same thing as their peers in the automotive industry. Some prostheses come with sensors to collect muscle data and adjust shock absorption accordingly.
RELATED: How various companies and industries embrace 3D rendering services and applications
They are almost robotic, with independent control for movement and grip. Starting prices are closer to $10,000 than to $1,000. For instance, Unlimited Tomorrow (one of the most well-known prosthesis manufacturers based in the U.S.) sells its prosthetic arm for nearly $8,000. Like most technologies, worldwide adoption is expected to impact prices. Lower manufacturing costs and readily available materials may permit the use of advanced prostheses in developing economies, where the devices are currently cost-prohibitive.
Development and Future
Manufacturing technologies for prosthetic devices have advanced significantly over the last 20 years. Much of the developments can be credited to CAD drafting services and 3D printing methods. It is not only about design visualization by a freelance CAD prosthetic designer on computers and additive manufacturing but also the engineering/invention of new materials to help with pressure dissipation and cushioning. Gel materials and carbon fiber composites, which have been used for decades in the automotive and shoe industries to produce parts, are also implemented into prosthetic manufacturing.
RELATED: How design firms use prototypes to develop critical new medical devices
In modern above-knee prosthetic limbs, the pylon also has a shock absorption mechanism to improve the patient’s biomechanical performance. Certain materials are water/moisture resistant, making the prosthetics suitable for beach or shower use.One of the most exciting studies in the field is the implementation of brain-controlled prostheses. The idea is to connect prosthetic devices with electrode arrays placed in the patient’s brain, muscles, or nerves to control limb movement. It is intended to allow the patients to control their prostheses in a much more naturally comfortable fashion.
Researchers at the University of Chicago are taking a step further by using touch sensors and brain-controlled mechanisms in prosthetic arms. With a combination of sensory feedback and natural movement, prosthetic devices – in the future – may function to enhance human physical abilities.
How Cad Crowd can help
Cad Crowd makes it easier than ever to connect with designers to help you develop your prosthetic arm, foot, leg, eye, or joint. We help clients with design for 3D printing, injection molding, or any other manufacturing technology. We also offer contract manufacturing services to help you get your product made. Contact us for a free quote.